|
|
Mixing Vessels, Tanks & Pipes
|
|
|
Click on any picture for a larger view.
|
|
Pipes
Pipeline Mixers, Pipe Mixer, In-line Mixing, Line Mixers, Line Blenders,
Process Intensifiers
These mixing containers are installed right in the pipeline. Ideal for
continuous processes or when a fluid component must be intensely mixed prior
to injection or addition into another mixing vessel. This is not limited to just
miscible fluids, but can also handle
liquid-liquid dispersions,
gas-liquid mass
transfer, or
solids dissolution. Its a great way to mix high viscosity fluids,
that are already being transported through a pipeline.
|

Example of a pipe being the mixing vessel.
Illustration by P. Csiszar
|
|
Vertical tanks
These are tanks standing upright. Mixers are most often mounted as top entering
or bottom entering, where they are mounted centrally on the base or top head of
the reactor. Some mixers are mounted on the heads, but off to the side. Most
common bottom entry off-center mounted mixers are the magnetic mixers. Most
common versions for top entry are off-center shafts parallel to the tank
walls (eccentric mixers), or angled toward the center as is the case with
most portable mixers.
|
Example of a top entry mixer on a vertical tank.
Illustration by P. Csiszar
|
|
Cylindrical tanks
Most common form of mixing vessel or chemical reactor in all of
the process industries. If nothing else is mentioned about a mixing tank, most
likely a metal vertical cylindrical tank is considered,
fully baffled. There are several types of heads
on cylindrical tanks.
- ASME dish: Standard and many variants
- Semi-elliptical dish
- Spherical
- Conical head
- Flat
Here is an example of a glass-lined vertical tank that has
been cut-out to show the interior. It has a
C-baffle and a pH-probe and 3 impellers all made of glass-lined steel.
|
Example of a top entry mixer on a glass-lined vertical tank.
Courtesy of Jürgen Reinemuth
|
|
Square tanks
Often square tanks are used based on materials of construction and expense.
Square tanks are often cheaper to build than cylindrical tanks. They are common
in phosphoric acid production, waste water treatment, and older mineral
solvent extraction plants. Often people erroneously assume that because the walls
are square, baffles are not needed. This is true for up to about 0.5 Hp/1000
gallons or 0.1 kW/m3. Above that and you need baffles to stop the swirl.
|
Example of a square tank made of cement for a copper solvent extraction process.
|
|
Vertical tanks with side-entry mixers
Another common mixer mounting practice is called side entering mixing.
Here the mixer is mounted on the tank walls, mostly near the base of the tank.
The petroleum and flood oil industry uses many of these, typically with just
one mixer per tank. Flue Gas Desulfurization (FGD) often has 3 or more mixers
per tank, either located all on one side (cluster arrangement) or evenly
spaced around the tank perimeter (symmetrical arrangement). Side entry mixers
can also be used in waste water treatment. They are typically found in large
volume squat tanks, where top entry would be impractical.
|
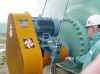
Examples of a side-entry mixer and orientation rules for the mounting of side-entry
mixers on a tank as a function of the number of mixers.
Courtesy of Philadelphia Mixers
|
|
Horizontal tanks
Cylindrical tanks are most common with dished heads. They are commonly
under pressure. In the mining industry they call these types of
vessels autoclaves. Autoclave reactors often have chambers inside of the tank,
each having one to three agitators, so that this continuous process mixer behaves
as several continuous stirred tank reactors (CSTR) in series. These types of
vessels can also be found skid-mounted or on a trailer and pulled or transported
by trucks.
|
Still looking for a picture of horizontal tanks.
If you would like to see your picture here with links to your site or to
your email address please let us know. |
|
|
 |
|